Why Manufacturing Matters At Cokebusters
10 April 2025
At Cokebusters, we do more than deliver world-class mechanical decoking and in-line inspection services. We design, engineer and manufacture the specialist equipment we use, entirely in-house. This integrated approach gives our clients in the energy industry a distinct advantage. From quality control and innovation to supply chain resilience and tailored solutions, our in-house manufacturing capabilities enable us to deliver reliable, efficient and future-ready services that meet the energy sector’s toughest demands.
Uncompromised Quality and Reliability
By manufacturing our own equipment, we maintain complete control over quality assurance. Every component is designed, built and tested by our own engineers and workshop teams, ensuring the highest standards of performance and reliability in the field.
Whether it’s a bespoke scraper pig manufactured at our premises in Houston TX or a Double Pumping Unit assembled at our UK Technology Centre, our tools are engineered with precision to maximise uptime and operational safety – even in the most demanding environments.
At our Technology Centre, we have a separate maintenance and manufacturing workshops. This enables us to ensure our existing fleet of machinery is attended to so each Double Pumping Unit can perform at full capacity, as well as producing new state of the art machines to introduce to the market. We are fortunate to have a dedicated team of skilled mechanical engineers, welder and fitters, as well as our the necessary equipment required to support our fleet of machinery.
Recently a machine returned from a client site with an engine severely damaged through running too hot for too long. Critically, the client’s job was completed successfully, just like a Formula 1 race the chequered flag was reached… time afterwards to make the necessary repairs. Back in the Cokebusters workshop the engine was stripped and rebuilt, putting the machine back into full service within 48 hours!
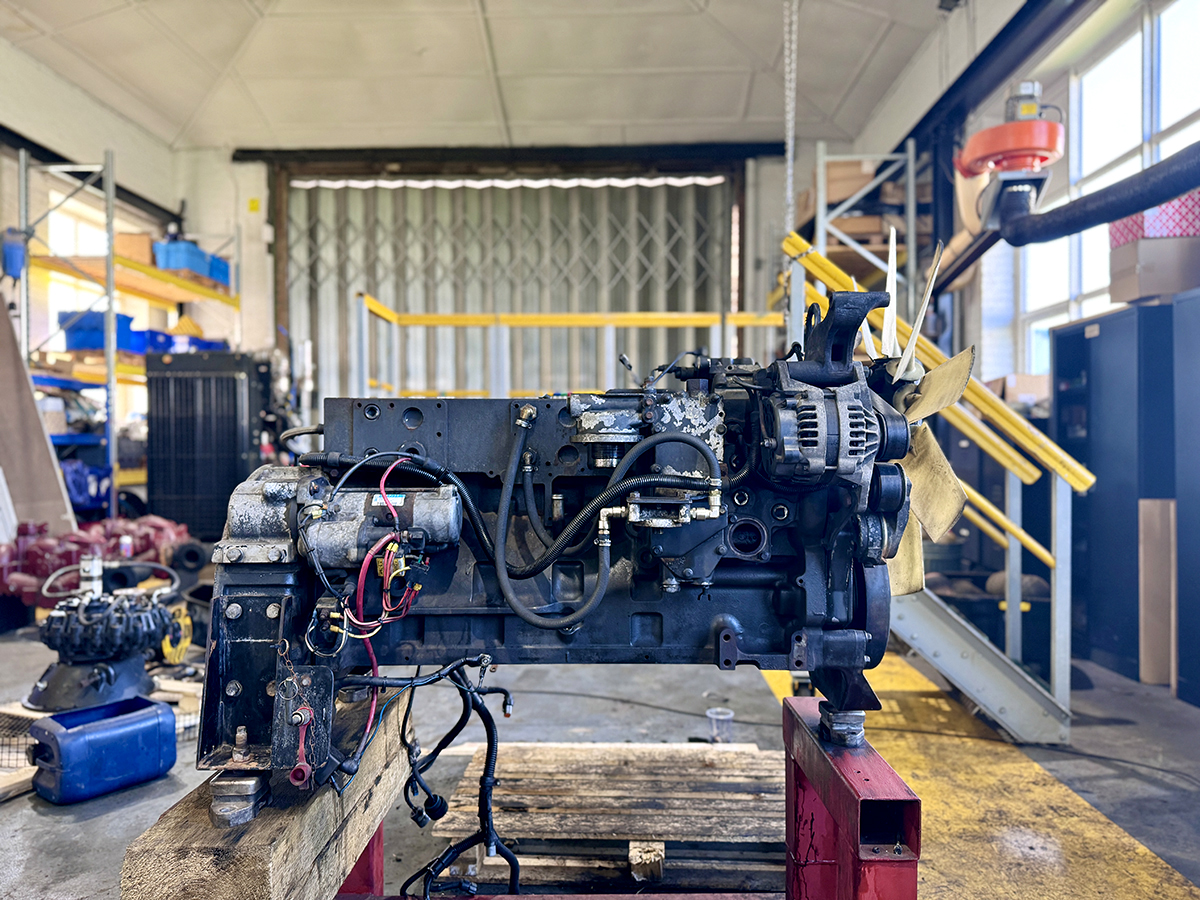
Continuous Innovation and Technological Advancement
Innovation is in our DNA. Because we build our own tools, we’re free to develop, test and implement new technologies without waiting on external suppliers or off-the-shelf solutions.
For example, our patented scraper pigs are designed and manufactured in-house, offering superior performance for coke removal, saving time and reducing risk. We also work with partners to develop bespoke systems, such as a custom-built polymer mixing and dispensing machine that has significantly increased our pig production capacity.
This flexibility allows us to rapidly evolve our tooling to meet new challenges and keeps our clients at the leading edge of industrial performance.
Customised Solutions for Unique Challenges
In the energy sector, no two sites or operations are alike. With full manufacturing control, we’re able to tailor equipment to suit specific client requirements, such as adapting pigs to handle unusual tube geometries.
By developing our own solutions, we reduce the need for mechanical modification on-site, avoid unnecessary downtime and ensure every job is completed as efficiently as possible.
Reduced Supply Chain Dependency
In an industry where timing is critical, delays can be costly and relying on global supply chains introduces risks that are often beyond your control.
By manufacturing our equipment internally, we’re able to eliminate unnecessary third-party dependencies. We control our own lead times, manage our own stock levels and ensure we have the resources available to meet demand, even in high-pressure or remote scenarios.
This supply chain resilience allows us to deliver projects on time and on spec, regardless of external disruptions.
Enhanced Safety and Environmental Responsibility
Every piece of equipment we produce is built with safety and sustainability in mind. Our Double Pumping Units include built-in safety features such as automatic emergency shutdown systems, spark arresters and acoustic enclosures to reduce noise exposure.
We’re also focused on environmental stewardship. From energy-efficient engine systems to the use of water filtration during decoking operations, our design process prioritises cleaner, more sustainable outcomes both for our clients and for the wider industry.
Seamless Integration of Services
Because we design and manufacture the tools we use, our operators and inspectors work with equipment they know inside out. This synergy leads to smoother operations, fewer errors and faster project delivery.
Our services – mechanical decoking, water filtration, cleanliness verification, tube inspection and integrity reporting – are not just aligned; they’re integrated. The result is a more efficient process, with better data and improved outcomes across the board.
A Smarter, Stronger Approach
At Cokebusters, we believe that making our own equipment makes us better at what we do. It means fewer delays, better solutions, and more control — all of which benefit our clients.
In-house manufacturing is more than an operational strength; it’s a strategic advantage. It allows us to respond quickly, think creatively and deliver the high standards of performance that energy clients demand every time.
Our business model of manufacturing in direct support of specialist combined service delivery isn’t easy… but we’ve been doing this for twenty years!
That’s why manufacturing matters.