Top 10 Questions Energy Plant Operators Have About Tube Cleaning
09 January 2025
Heat exchangers and condensers are the heart of any energy plant and their efficiency is critical to the plant’s overall performance. Keeping the tubes in these systems clean ensures optimal operation, reduces downtime and extends equipment lifespan. However, plant operators often have questions for us about when and how to clean their tubes.
In this article, we’ll address the top 10 questions energy plant operators commonly ask about tube cleaning, so you can stay ahead of maintenance challenges and keep your systems running smoothly.
1. What are the main signs that my tubes need cleaning?
The most common signs include:
- A drop in heat transfer efficiency.
- Increased energy consumption as systems work harder to compensate for fouling.
- A noticeable throughput pressure increase in your system.
- Visual signs of buildup during routine inspections.
If you’re noticing any of these issues, it’s time to act before the situation escalates.
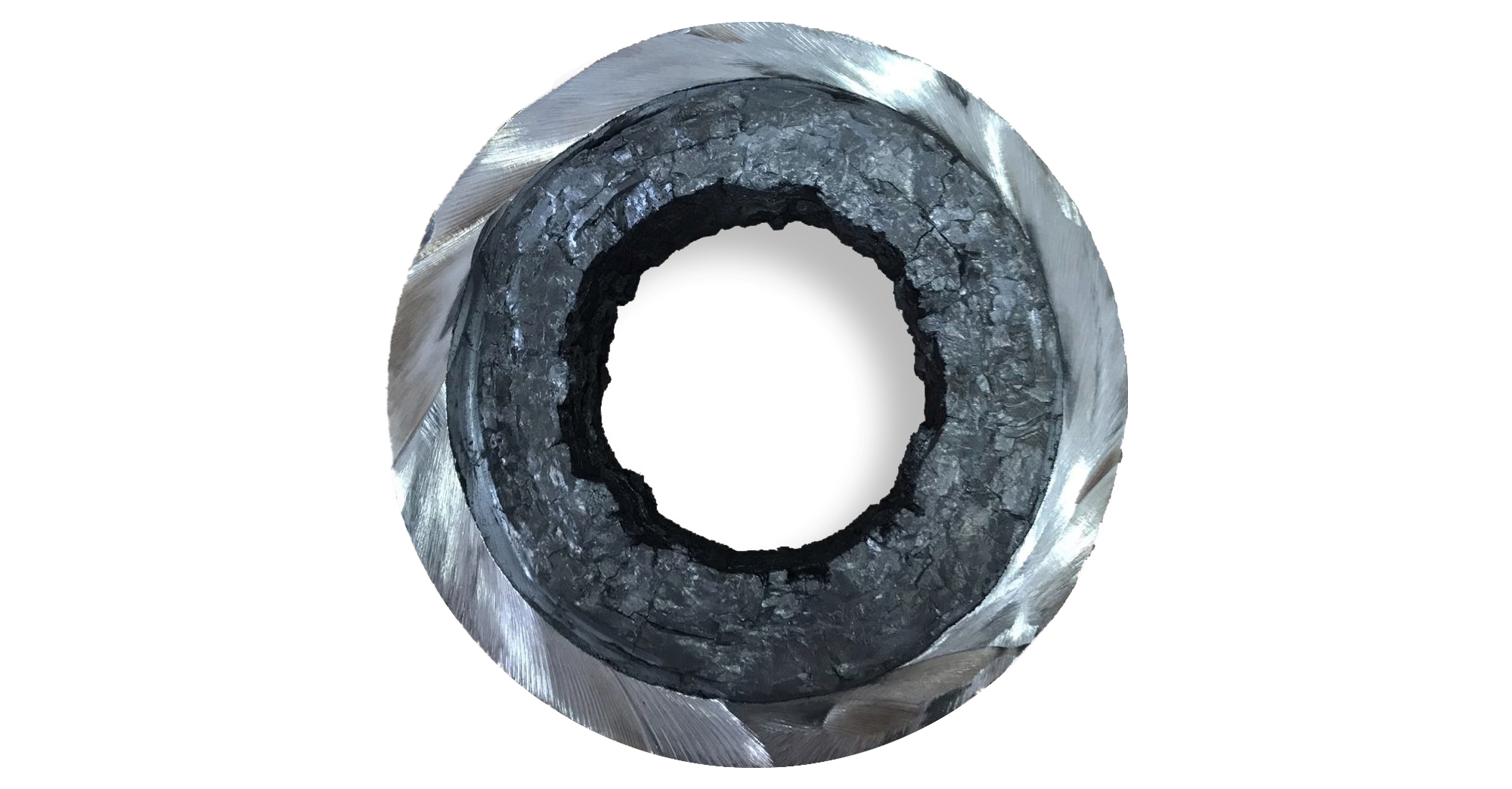
2. How often should we clean our tubes?
The frequency of cleaning depends on several factors, such as the type of energy plant, operating conditions and the quality of the fluids passing through your system. Cleaning schedules can range from annually to every few years, depending on usage and fouling rates.
It’s important to base your schedule on real-world data and inspections, rather than a one-size-fits-all approach.
3. What’s the difference between mechanical and chemical cleaning?
Mechanical cleaning uses physical tools like brushes, scrapers or high-pressure water to remove deposits. This method is effective for removing any heavy fouling and scale buildup in a wide variety of assets.
Chemical cleaning involves the use of specialised solutions to dissolve deposits. It’s only suitable for soft fouling in delicate systems and results in harsh chemical waste causing risk of environmental contamination.
Steam air decoking uses high-temperature steam to loosen and remove light deposits, oils and biofilms. This is a traditional method of injecting steam into the tube circuit, driven by compressed air. It known to be skill sensitive, meaning that it has to be carried out by skilled and experienced personnel. The process is actually quite effective when done correctly, although it is broadly understood that it typically does not remove inorganic material.
It works for certain applications, but is largely ineffective when addressing heavy fouling and can dislodge fine particles, contaminants or hazardous residues from tube surfaces, potentially releasing them into the air.
4. How can I prevent tube fouling in the first place?
While fouling often can’t be avoided in the long-term, it can be minimised or slowed by:
- Maintaining proper water treatment systems to reduce contaminants.
- Installing filtration systems to capture debris before it enters the tubes.
- Avoiding the process of poor quality oils. Whilst it can sometimes seem like a good financial decision, will lead to an early build up of coke.
- Regularly monitoring and cleaning to prevent buildup from becoming severe.
Prevention is always more cost-effective than remediation. Regular and good quality decoking is very important to maintain and extend long run lengths. If a tube interior is not cleaned fully during a mechanical cleaning operation, this will likely cause a more rapid build up during the next operational run. The ideal policy is to carry out competent decoking and use a tube inspection for coke removal verification. That way clean tubes are a certainty, leading to a good and efficient next run period. This sort of treatment is also likely to prolong tube life.
5. How does tube fouling affect my plant’s energy efficiency?
Even a small amount of fouling can significantly reduce heat transfer, forcing your systems to use more energy to maintain the same output. This translates directly into higher operating costs and reduced efficiency. Clean tubes allow your plant to operate at peak performance and reduce unnecessary energy consumption.
6. What tools and technologies are used in the Cokebusters mechanical cleaning service?
All our tools and equipment are designed and purpose-built in house. These include:
- Cokebusters specialist Double Pumping Units, which drive water pressure to push our mechanical pigs through two passes at a time.
- All associated hoses and parts required to connect to the asset.
- Patented scraper pigs designed to remove tough deposits.
These technologies ensure cleaning is thorough, efficient and minimally disruptive.
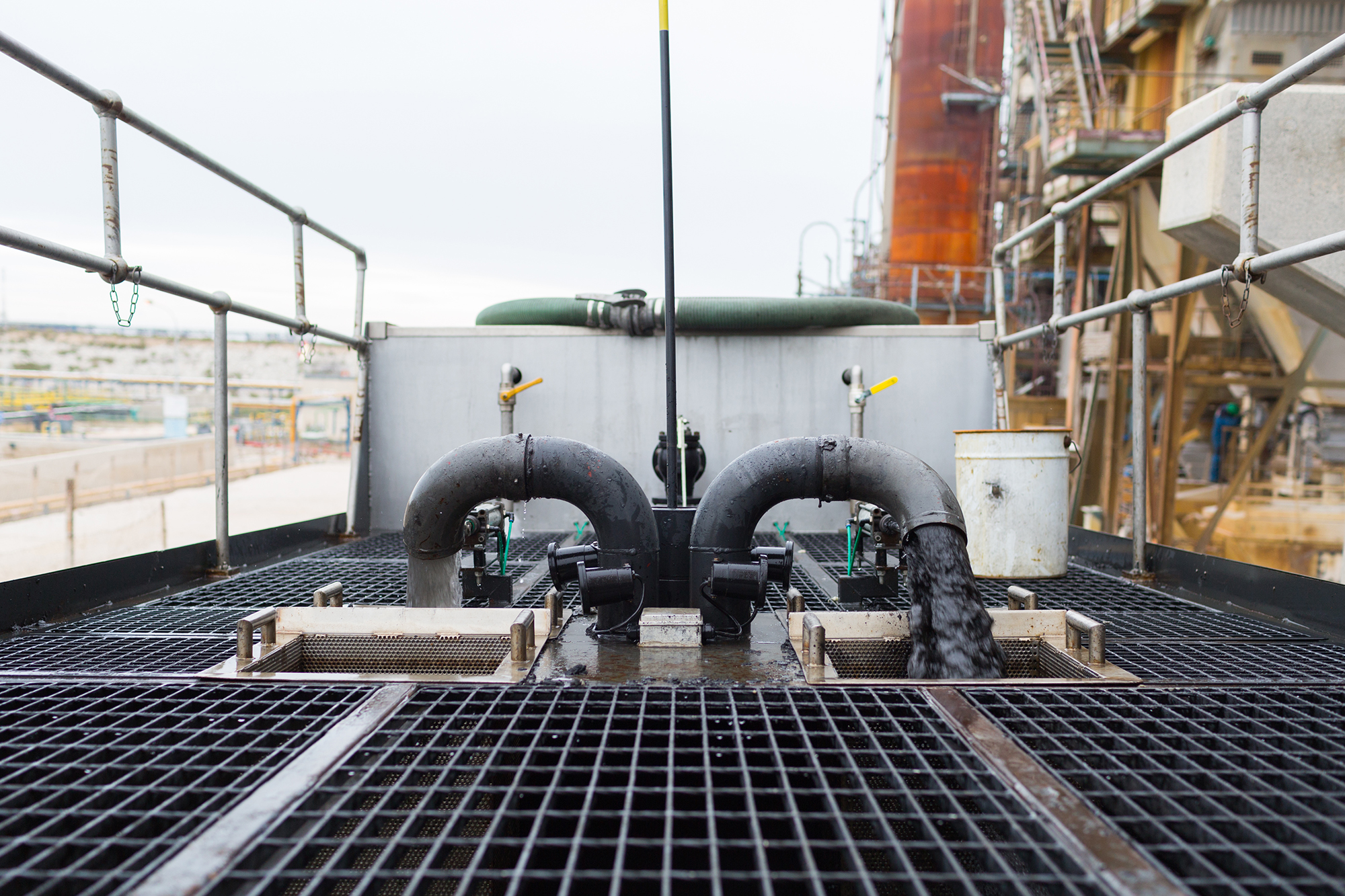
7. How long does the tube cleaning process typically take?
The duration depends on the size of the system and the extent of fouling. For most furnaces and fired heaters, cleaning can be completed within two to three days. Advanced planning and preparation can minimise downtime.
8. How does regular cleaning impact equipment lifespan?
Regular tube cleaning prevents fouling-related corrosion and wear, which are leading causes of tube failure.
As a tube becomes coked internally, the furnace temperature has to be increased in order for the heat to reach the oil. An internal coke layer acts as an insulator, so the operator must ‘turn up the gas’ which is more costly in fuel. Overcoming the insulating layer in this way means the tube metal has to be heated to a higher temperature. There are tolerances which allow such increase, but as the skin temperature increases so the tube life decreases. In extreme circumstances tubes will suffer degradation which is very costly, ending up with replacement of tubes.
By keeping tubes clean, you’ll not only maintain performance but also extend the lifespan of your equipment, saving money in the long run.
9. Is tube cleaning disruptive to plant operations?
While tube cleaning does require some downtime, proper scheduling and preparation can minimise disruption. Many service providers, like us, offer flexible scheduling options and use efficient cleaning technologies to reduce the impact on your operations.
10. What should I look for in a tube cleaning service provider?
Key factors to consider include:
- Experience in servicing energy industry clients.
- A track record of minimising downtime and delivering measurable results.
- Commitment to safety and regulatory compliance.
- The ability to offer a combined service of mechanical cleaning coupled with subsequent inspection services.
Choosing the right provider ensures your equipment gets the care it needs without compromising plant performance.
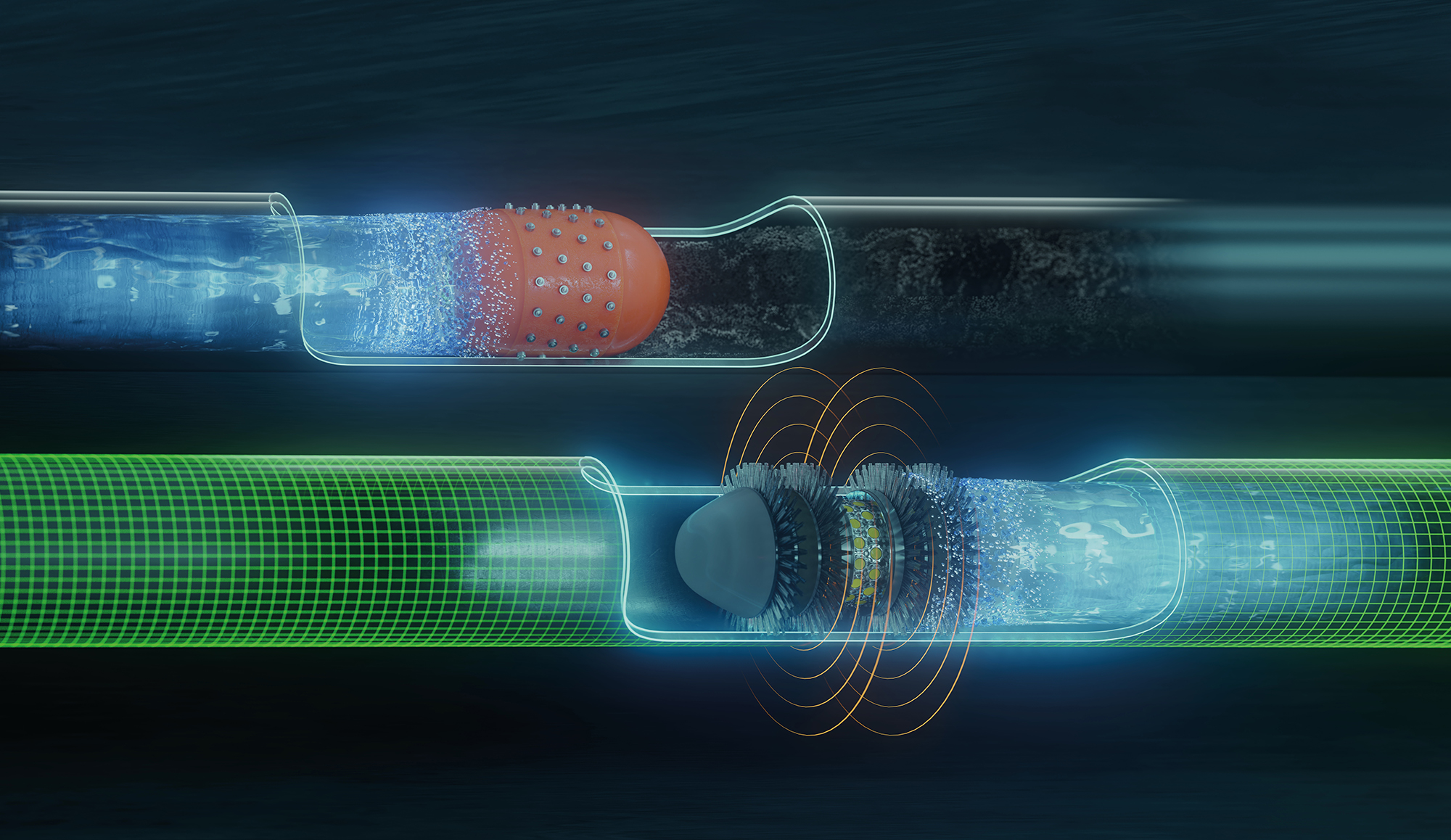
Conclusion: Keep Your Tubes (and Plant) in Top Shape
Mechanical cleaning is a critical part of maintaining energy plant efficiency and profitability. By understanding the process and addressing these common questions, you’ll be better equipped to make informed decisions about your maintenance schedule and service providers.
It is natural for decision-makers with their eyes focussed on contractor bid prices to be inclined to award a mechanical cleaning contract to the cheapest provider. Although this is enticing, if that provider fails to conduct the works in a professional, competent, safe and time efficient manner, the result is often much more costly in the long-term. Our longstanding clients understand this trade-off and encourage their purchasing and operations teams to work closely together during this selection process.
If you’re ready to optimise your heat exchanger and condenser performance, contact us today to learn how our expert team can help keep your systems running smoothly.